The fourth industrial revolution is upon us and it’s bringing with it a host of technological advances, including artificial intelligence (AI) and robotics. With AI and robots entering the manufacturing space, the question arises: Will they replace human labor? This article takes an in-depth look at the impact of AI and robots on manufacturing workers to answer this question.
The article examines whether or not AI and robots have already begun replacing humans in the field of manufacturing. We explore how these technologies are changing working conditions for employees as well as what implications this may have for society going forward. By examining current trends and developments we hope to gain insight into just how far down this path we’ve gone – and where we might be headed next.
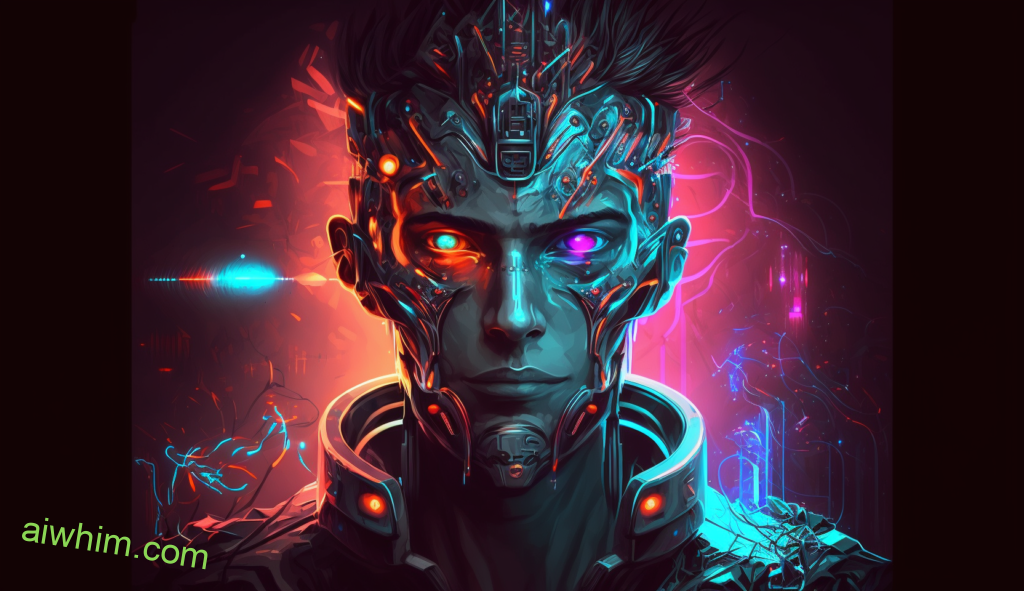
Before we start, this article is about AI and job risks particularly in manufacturing. If you are instead interested in AI’s impact on warehouse work, read the linked article instead.
Definition Of AI And Robotics
Are we headed for a future where robots take over the world? It might seem far-fetched, but with the rise of artificial intelligence (AI) and robotics in manufacturing, it’s no longer just science fiction. AI and robotics are quickly becoming an integral part of modern production systems, bringing increased efficiency and automation to many industries. But what is AI exactly, and how does it differ from robotics?
To understand these two concepts, let’s start by defining them. A robot is a machine designed to carry out specific tasks autonomously or semi-autonomously; they can be programmed to follow certain commands or behaviors without human intervention. Artificial intelligence is the ability of machines to learn from their environment and adapt accordingly. Unlike traditional programming techniques that rely on explicit instructions, AI uses algorithms and statistical models to enable computers to “learn” from data sets. In other words, AI allows machines to develop problem solving skills based on experience rather than being explicitly told how to do something.
While both technologies have tremendous potential in manufacturing processes, there are significant differences between them: Robotics focuses primarily on physical labor while AI enables machines to make decisions independently–enabling smarter automation solutions for industrial applications such as predictive maintenance and automated quality control. Ultimately, this combination of robotic hardware and intelligent software has enabled manufacturers around the globe to increase productivity while reducing costs.
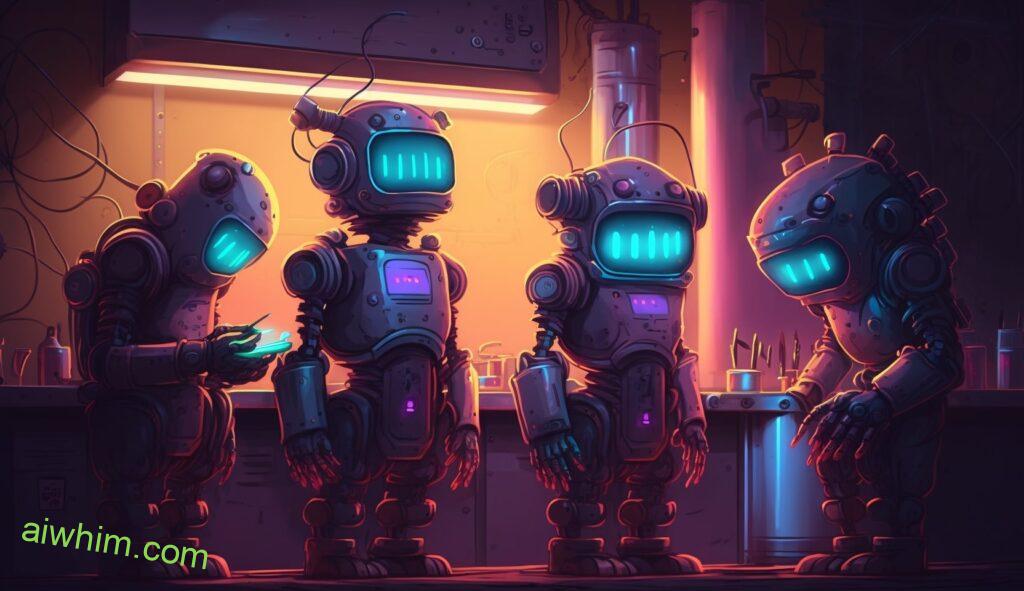
You may also want to read this article about how AI disrupts construction jobs. (Click the link to read!)
History Of Automation In Manufacturing
The history of automation in manufacturing is rooted in the industrial revolution. Automation has been used to reduce labor costs and increase productivity since that time. It has also increased safety, allowing workers to work with less risk.
In the early days of automation, machines were used to replace manual labor for simple tasks such as sorting items or packaging goods. As technology advanced, robots began to take over more complex jobs, like welding and assembly line production. This allowed manufacturers to produce products faster and cheaper than ever before.
Today, automated systems have taken on even more roles in manufacturing. AI-controlled machines can process data quickly and accurately so they can make decisions without human intervention. These advances have made it possible for factories to operate 24 hours a day with minimal human input. The result? Production speeds are higher than ever before while labor costs remain low. With these developments, it’s clear that automation will continue to play an integral role in modern manufacturing processes.
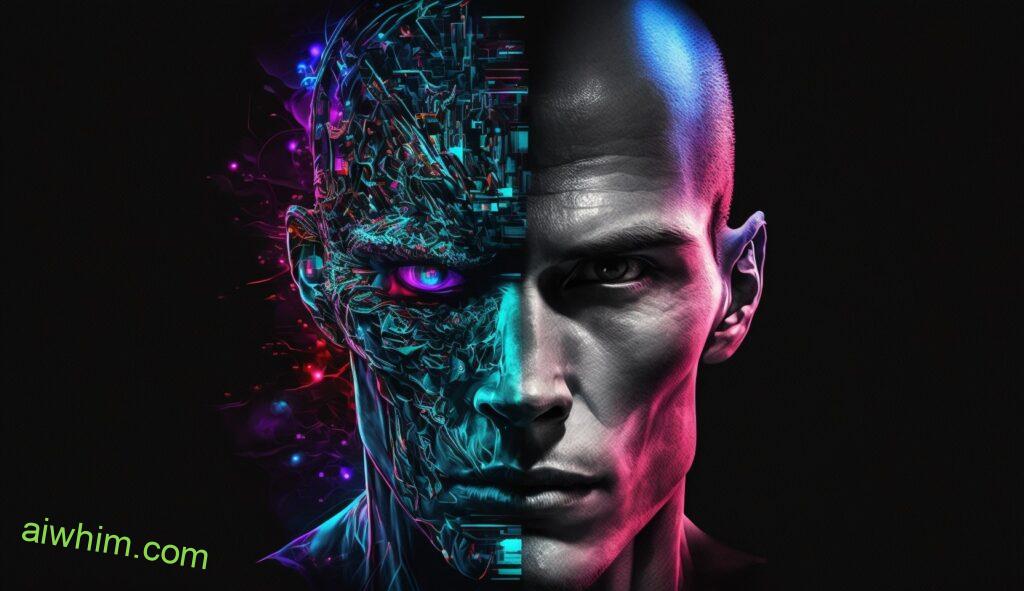
Benefits Of Automation
When it comes to automation, the benefits are simply mind-blowing! The manufacturing efficiency that robots and AI can bring to an industry is unparalleled. With production speeds skyrocketing, labor costs plummeting, and cost reduction strategies becoming more efficient than ever before, it’s no wonder these technologies have become so popular in recent years.
The advantages of automating a manufacturing process cannot be understated. By replacing manual labor with machines or software, organizations can drastically reduce labor costs while increasing production speed and accuracy. This not only makes processes faster and simpler for employees but also helps companies save money on staffing expenses as well as materials used in the production process.
Moreover, automation has enabled manufacturers to stay competitive by reducing errors in their products and services. Automated systems can detect potential problems early on and alert staff members to take action before any damage occurs. As a result, businesses are able to produce higher quality goods at lower prices due to reduced waste from mistakes and improved productivity overall.
There’s no denying that automation is revolutionizing the way we do business today – allowing us to achieve maximum efficiency without sacrificing quality or customer service. And what’s more? We get all this benefit without having to sacrifice our freedom – something which we all crave deep down inside.
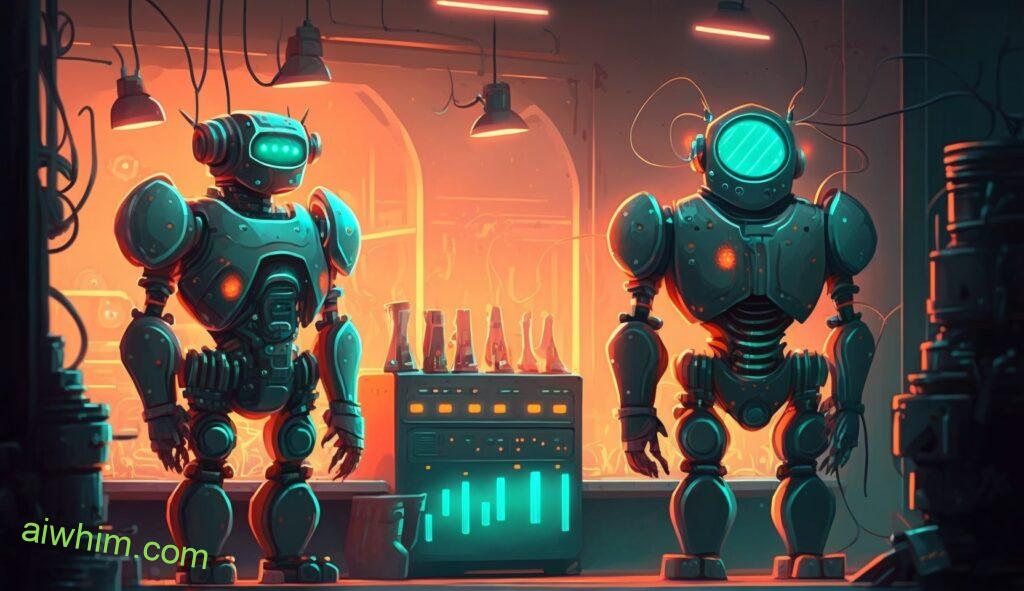
Drawbacks Of Automation
Despite the many benefits of automation, there are still a few drawbacks that must be considered. Automation has been proposed as a possible replacement for manufacturing workers in various industries. While this may bring cost savings and efficiency gains to businesses, it could also have an adverse effect on job security and worker safety.
Here are five ways automation can impact job security:
- Increased competition among employees vying to get their jobs automated away first
- Reduced wages due to fewer opportunities available
- Loss of specialized skills that robots lack the ability to perform
- Lack of diversity in roles and tasks within the workplace
- Limited advancement opportunities caused by limited manual labor positions being replaced with machines
Moreover, despite improved safety protocols, there is still some concern over potential risks associated with automation technology. Workers may face exposure to hazardous materials used in robotics production or contact with malfunctioning robotic equipment during operation. This could lead to serious injuries if not handled properly. Additionally, there are economic concerns related to automation investments—they require large amounts of capital upfront which can be difficult for small businesses and startups to acquire.
Overall, while automation does offer advantages like increased productivity and cost savings, it comes at a price that should not be overlooked when considering its implementation in any organization or industry. It’s important for employers to weigh both sides carefully before making a decision about how they want to approach automating their business processes.
Potential Implications On Workers
The introduction of AI and robots into manufacturing is sure to have an immense impact on workers. Inevitably, the presence of these technologies will result in job loss for some displaced workers. However, with careful planning, companies can work to ensure that employee retention remains a priority.
Organizations must be proactive when it comes to helping employees transition their careers in light of advances made by technology. Providing access to training opportunities and resources can help individuals develop skills necessary for success in different fields or industries. This will allow them to stay competitive within the labor market and expand their employment prospects.
Though there may be a period of upheaval while this transformation takes place, ultimately we can expect a more robust working environment going forward. By offering comprehensive support systems, organizations can mitigate potential issues associated with technological change and create an atmosphere conducive to long-term growth and development – one where each individual’s contribution is valued.
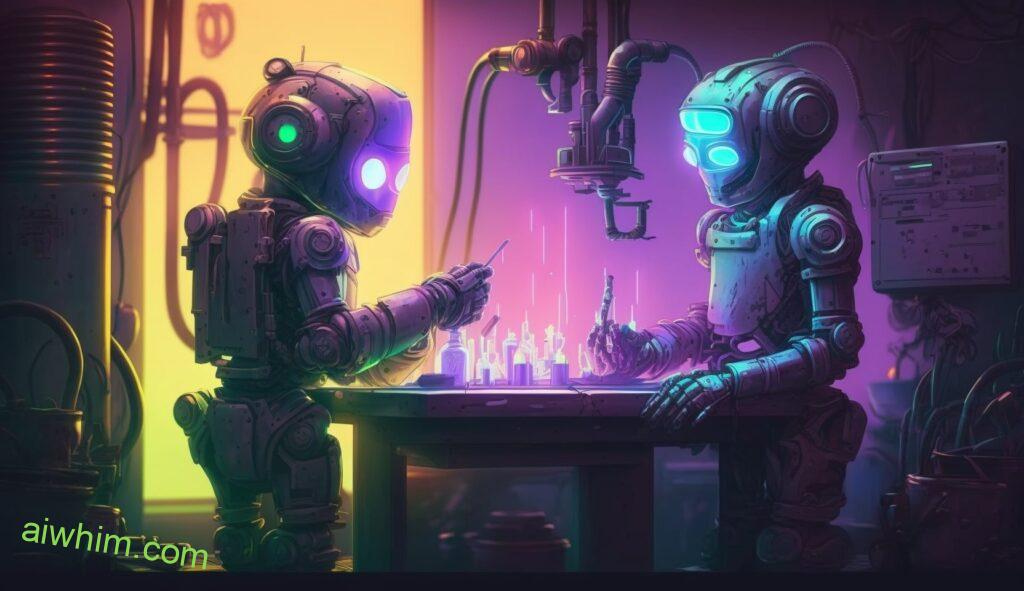
Impact On Job Market
The potential implications of the use of AI and robots in manufacturing are far reaching, with many asking whether these technologies will replace human labor. The impact this could have on the job market is a cause for concern, as automation could lead to an increase in unemployment rates due to companies preferring machines over workers. Automation can also affect industry labor through increased wages, as employers may need fewer employees to do the same amount of work that would otherwise require more people if done manually.
AI and robots could therefore dramatically change how jobs are performed in the manufacturing sector; resulting in greater efficiency but at what cost? Job opportunities in manufacturing could decline significantly, leading to a decrease in employment prospects for those looking for such positions. Furthermore, certain skillsets required by some roles might be replaced by automated processes resulting in further job losses or redundancies within specific sectors.
Automation has been seen throughout history as both beneficial and detrimental; however it’s clear that its introduction into the manufacturing industry has significant implications for the job market. From reducing manual labor costs to replacing certain skilled roles with robotic technology, there is no doubt that it will continue to play a larger role going forward- impacting not only manufacturers but their workforce too.
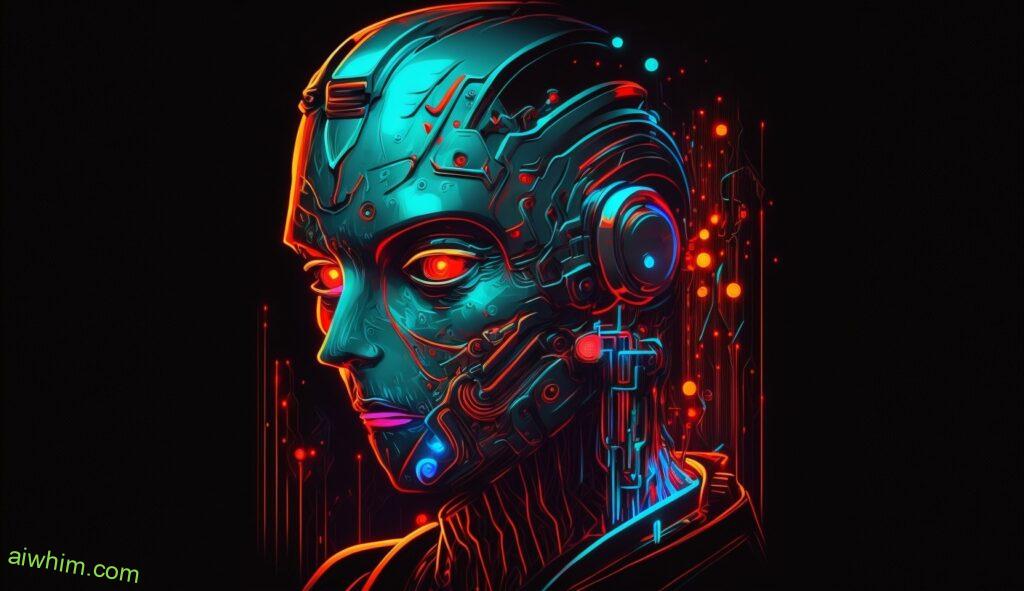
Role Of Government
The role of government in addressing the issue of robots and AI replacing manufacturing workers is an important one. Governments have a responsibility to ensure that their citizens are adequately protected against potentially disruptive technological changes, particularly those that threaten employment opportunities. To this end, governments can intervene by providing regulation to minimize job displacement due to automation or robotics. Government action could also include offering incentives for companies to invest in technologies which create new jobs alongside existing ones, as well as implementing policies designed to strengthen labor rights so that workers’ livelihoods are better secured.
Moreover, governments should take proactive steps towards preparing citizens for the changing nature of work through education programs focused on teaching skills such as coding and digital literacy. By doing so, individuals will be more likely to benefit from the increased potential for job creation associated with robot-enabled industries rather than suffering its ill effects. Additionally, it would help bridge any gaps between current abilities and employer needs while giving people access to alternative career paths if they find themselves out of a job due to robotic automation.
It’s clear then that the government has an essential part to play when it comes to navigating the transition from traditional manufacturing methods into automated production processes. It is only through appropriate intervention and policy implementation that we can secure our collective economic future whilst ensuring that all members of society are able to share in its benefits.
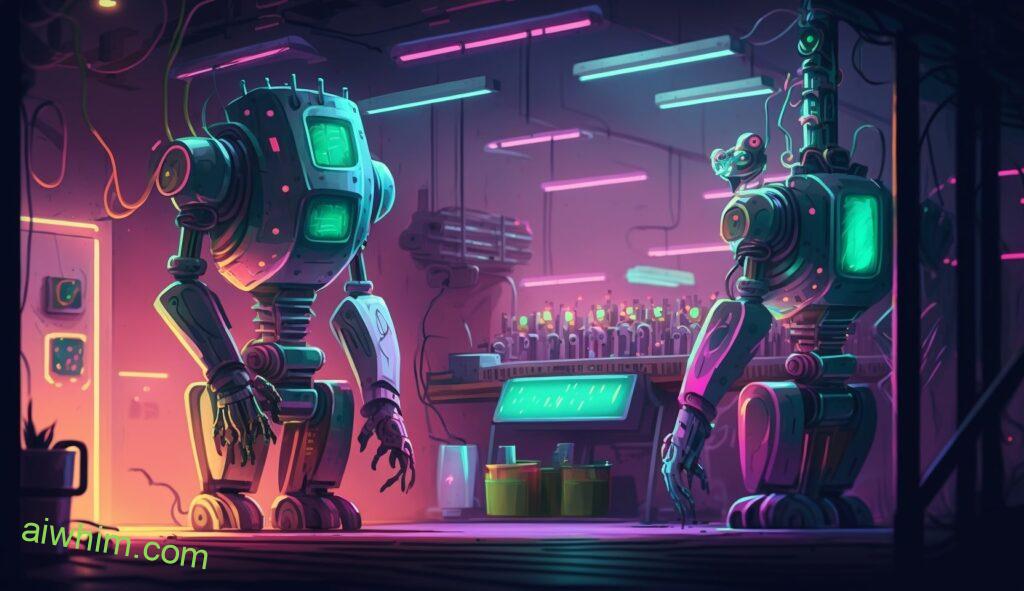
Employment Opportunities In Related Fields
The future of work looms on the horizon like a dark cloud, with the potential to disrupt traditional employment opportunities. Yet it could also be seen as an opportunity for career growth and advancement in related fields. As manufacturing workers face uncertain job prospects due to AI and robots taking their place, they should consider exploring:
- Training programs tailored to their specific skillset
- Job openings at companies that utilize cutting-edge technology
- Career prospects in fields such as data analysis or IT support
- On-the-job training through apprenticeship programs
- Online courses designed to help them stay ahead of the curve
By gaining knowledge and experience in these areas, former manufacturing employees can discover new pathways toward economic freedom. With access to modern tools, updated resources, and valuable connections made along the way, this transition can open doors to professional success. Achieving financial independence is often times a matter of investing time into meaningful pursuits; ones which offer both personal satisfaction and tangible rewards. So why not explore the possibilities? Who knows what kind of great things await you!
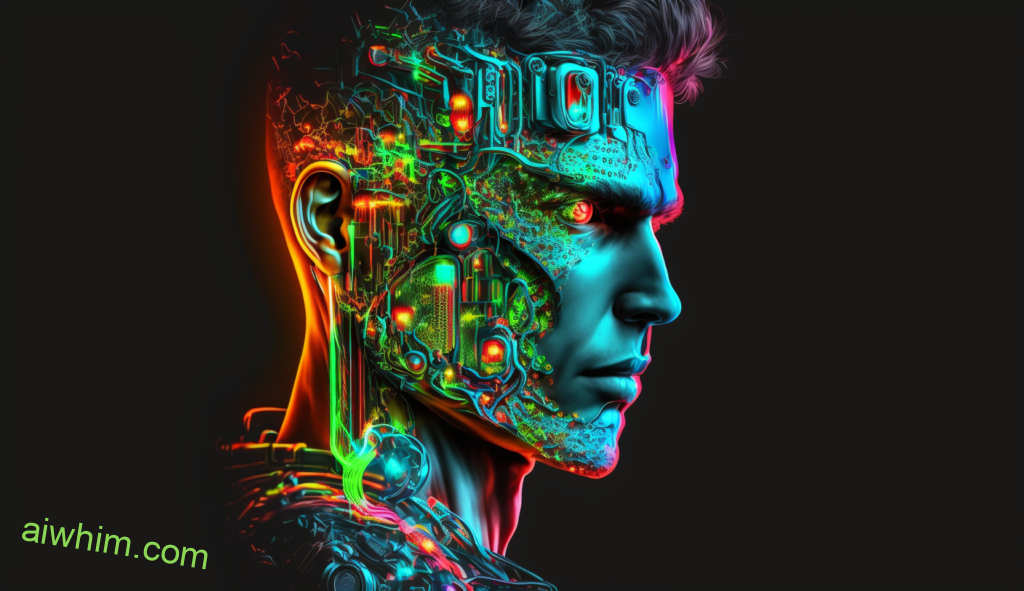
Education Requirements For New Occupations
As the world of manufacturing evolves, so must the education requirements for new occupations. With advancements in AI and robotics changing how products are produced, there is an increasing need to acquire essential skills that will qualify individuals for jobs more closely related to artificial intelligence or robotics. Training requirements have become increasingly strict as employers look for candidates who can meet their standards with regards to technology-related qualifications.
Traditional educational programs may not be enough when it comes to finding employment in this field, as most educational institutions lack the necessary resources and instructors who specialize in these newly created positions. As such, many people find themselves relying on independent sources or private organizations to gain the knowledge they need. From online tutorials to specialized courses; all of these options provide access to a wealth of information that could help make someone competitively qualified for certain roles.
The future job market has already started shifting towards one where technology plays a major role and those who stay ahead of the curve by investing time and effort into learning can reap great rewards from it. It’s important then, that we put our best foot forward when it comes to preparing ourselves for today’s ever-changing workforce and equip ourselves with the skills needed to succeed in any industry. With dedication and perseverance, anyone can position themselves well within emerging markets – no matter what profession!
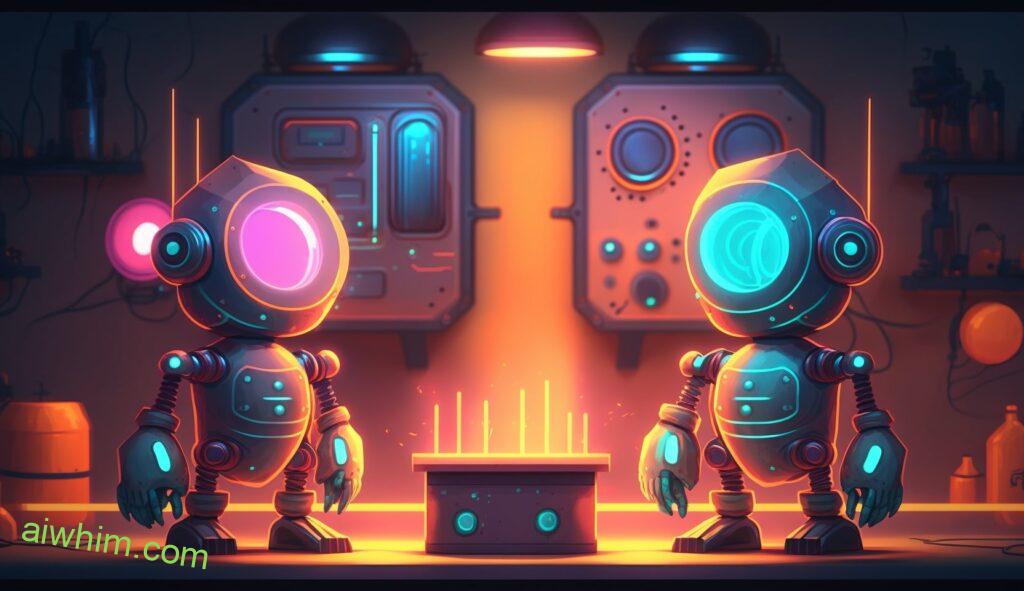
Ethical Considerations
When discussing the potential of AI and robots to replace manufacturing workers, ethical considerations must be taken into account. This looming shift has serious implications on how society values labor, worker rights, and automation ethics.
First, any form of automation should not put people in harm’s way or cause them to suffer financial loss due to job displacement. Automation also needs to be managed responsibly so that it doesn’t create an economic divide between those who can access technology and those who cannot.
Second, workers need to have a say in their own future when it comes to automation. They should be consulted on decisions about which jobs are automated first and what kind of safety measures will be implemented for those affected by automation-related layoffs. Additionally, there needs to be adequate training opportunities provided for employees whose roles may change due to new technologies being introduced in the workplace.
Finally, these changes require us all – employers and employees alike – to understand our shared responsibility towards each other as well as the planet:
- We must ensure fair wages and working conditions for everyone involved with manufacturing processes;
- We must prioritize sustainability initiatives that minimize environmental impact;
- And we must acknowledge the long term value of human creativity over short-term cost savings through robotics.
It’s clear that while AI and robots offer great potential for efficiency gains in manufacturing, they come with a moral obligation too. As such, governments around the world need to collaborate closely with businesses and labor unions in order develop policies that balance innovation with social justice – ensuring the right outcomes for all stakeholders at every step of this process.
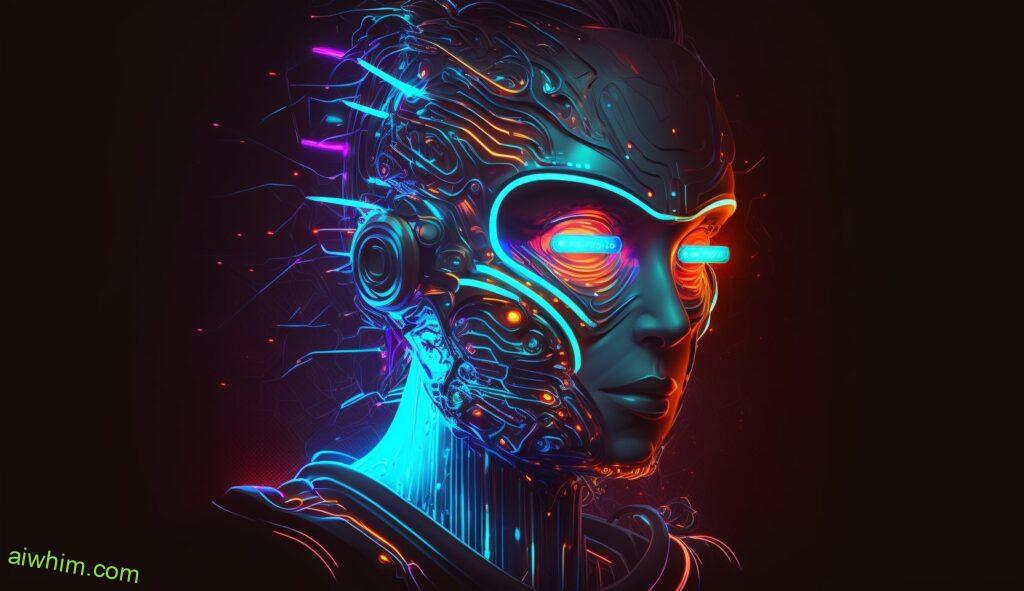
Comparison To Previous Technology Advances
The ethical considerations of automation replacing human labor discussed previously leave many questioning the effects that robots and AI will have on our society. In order to better comprehend how this technology could impact us, it is important to look back at previous technological advances and compare them to what we are faced with today.
During the industrial revolution, for example, steam engines replaced horses in transportation and production processes became more efficient. This allowed for a greater amount of goods produced at lower costs due to increased automation. However, despite these cost savings, the labor force was drastically impacted through job losses and overworking of those who remained employed.
Today’s situation seems quite similar when considering the potential impacts of robots and AI taking jobs from humans. Automation has already been seen as an attractive option for businesses looking to save money by reducing production costs; however, this means fewer positions available for workers across all industries which can lead to decreased wages or unemployment altogether. As such, it is essential that governments take steps towards protecting their citizens before fully embracing this new form of technology.
Though there may be some initial bumps in the road ahead with adoption of robotics and AI becoming mainstream in manufacturing environments, history tells us that eventually these technologies bring progress while also allowing people more time freedom than ever before – something everyone desires deep down.
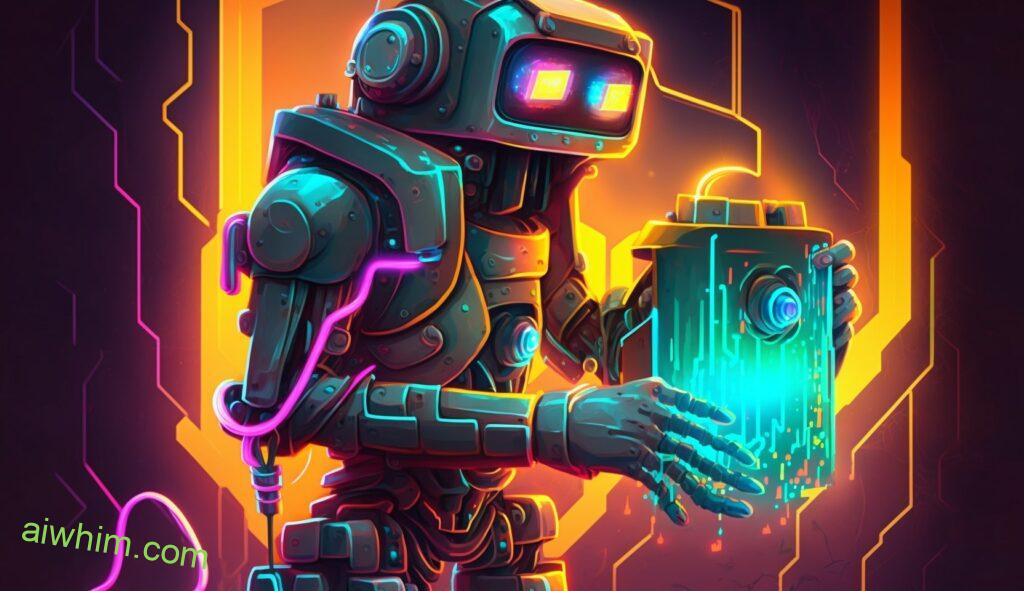
Adoption Rate Projections
The adoption rate of robots and artificial intelligence (AI) in manufacturing is projected to increase significantly in the coming years. According to recent industry reports, automation and robotics are expected to account for more than 50% of global manufacturing by 2030. This means that most manual labor jobs will be replaced with automated systems or machines operated by AI algorithms.
This shift towards robotic automation has already begun in many industries across the world, particularly those dealing with high-volume production processes. For example, automotive factories have been using robots for decades now but their use has become even more pervasive as manufacturers seek higher levels of efficiency and accuracy from their operations. Similarly, AI has also been used extensively in food processing plants for tasks such as packing, sorting and labeling products.
As technology continues to advance at an exponential rate, it is likely that a much larger proportion of manufacturing workers will eventually be displaced by robots and AI over the next decade or two. However, there may still be opportunities for human workers to help operate these automated processes under certain circumstances; especially where creativity and problem solving skills are required. Ultimately though, the future of work in this field lies firmly within the realm of automation and robotics adoption rate projections.
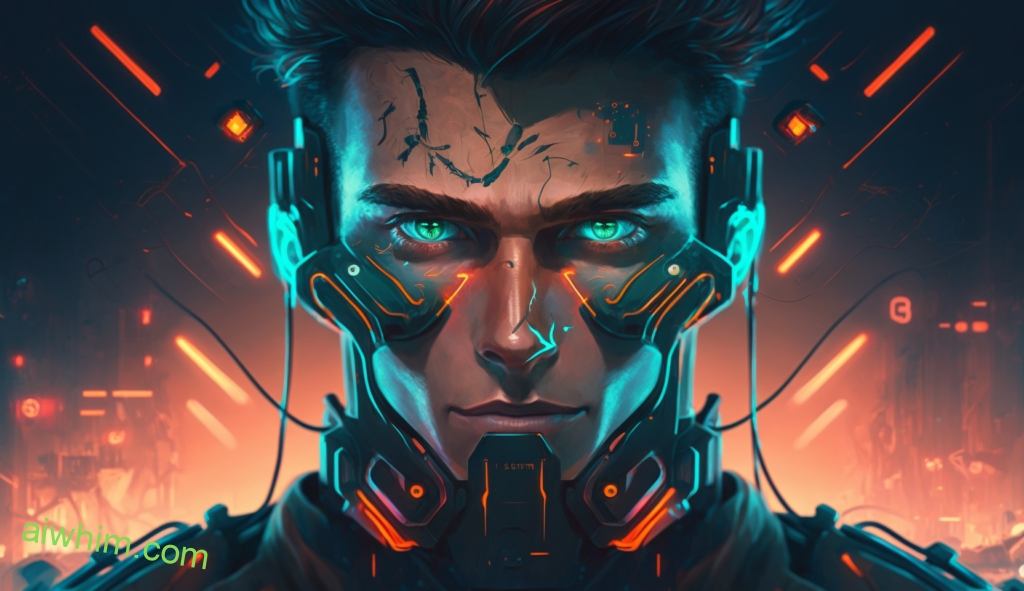
Mitigation Strategies For Displaced Workers
The emergence of artificial intelligence and robotics in manufacturing has left many workers feeling like they’re standing on the edge of a cliff, gazing into an abyss. It’s no surprise that mitigation strategies are needed to help protect those whose livelihoods may be at risk due to automation.
One method is worker retraining. Job market opportunities must be identified for displaced workers so they can acquire new skills and convert their existing ones for use in other industries. This could include providing vocational or technical training and tuition assistance to assist with skill development and certification. Governments could also provide employment assistance programs such as job search support, resume writing services, interview coaching, and career counseling.
In addition, governments should consider implementing initiatives to encourage companies to hire displaced workers by offering incentives such as tax credits or access to grants. There would also need to be a focus on creating more jobs through investment in infrastructure projects or supporting small businesses which have traditionally been drivers of economic growth in countries around the world.
It’s clear that there are several options available when it comes to mitigating the impact of automation on displaced workers’ lives. By taking proactive steps now, we can ensure these people don’t just become another statistic but instead receive the necessary support they require while transitioning into their next chapter – whatever form that may take!
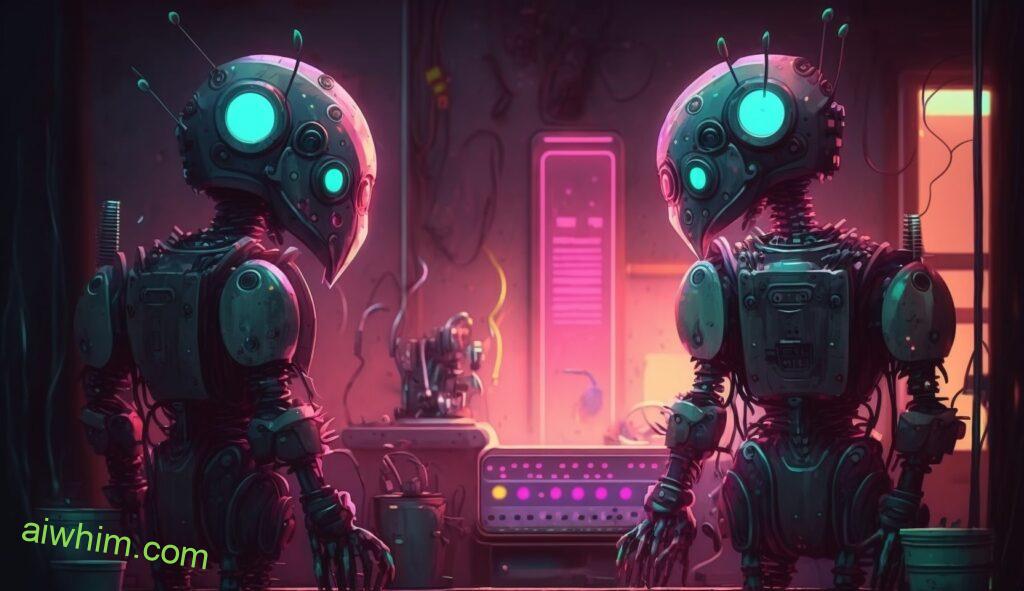
Potential For Job Creation
The potential for job creation due to the development of AI and robots is a complex issue. While automation offers many benefits in terms of efficiency, cost savings and improved product quality, it also has its drawbacks which could potentially displace workers. On one hand, robotic programming and AI are expected to create new jobs in software engineering, electrical engineering and computer science as well as other related fields. On the other hand, some jobs that were once done by human beings may increasingly become automated or replaced with robots.
It is important to recognize that these changes do not necessarily mean fewer jobs overall – there will still be plenty of opportunities for people who are able to adapt their skillset to take advantage of these new technologies. For instance, those working on robotics-related projects can gain experience in areas such as machine learning algorithms and data analysis. In addition, companies have an opportunity to benefit from reduced costs associated with labor while at the same time creating more efficient processes through automation technology.
Despite this potential upside, there are still concerns about how automation might affect humans’ ability to find work in traditional roles. Governments should consider introducing policies that help support displaced manufacturing workers so they can transition into emerging industries where their skillsets may be applicable. This could include providing training programs tailored towards preparing individuals for future job requirements within rapidly changing environments caused by technological advancements.
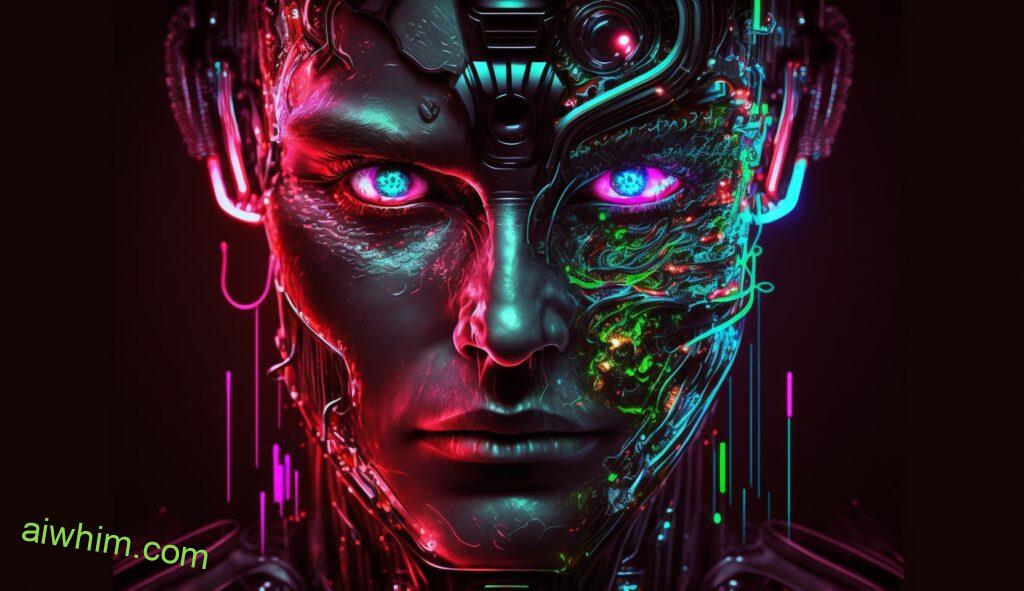
Outlook For The Future
The outlook for the future of manufacturing jobs is complex and hard to predict. Automation has already had a significant impact on how manufacturing processes are carried out, and this trend is likely to continue in some form or another. However, while automation may take over certain aspects of the job, there will still be an ongoing need for human employees with specialized skills that robots can’t replicate. To ensure long-term success, it’s important to invest in training and development opportunities so workers can stay ahead of advances in technology.
Data suggests that despite increased automation, many areas within the field of manufacturing have seen steady growth in recent years. This indicates that even as machines become more integrated into production lines, they won’t necessarily replace humans entirely – rather, they’ll help reduce labor costs while allowing companies to increase their output at the same time. Moreover, since new technologies often require staff members with specific qualifications or expertise to operate them properly, demand for qualified professionals could remain high.
In short, although much of what happens inside a factory today is automated or machine-run, there will always be a place for talented people who possess unique combinations of knowledge and experience. By continuing to hone their skillsets and staying abreast of industry trends and developments, those interested in pursuing a career in manufacturing should find plenty of opportunity ahead.
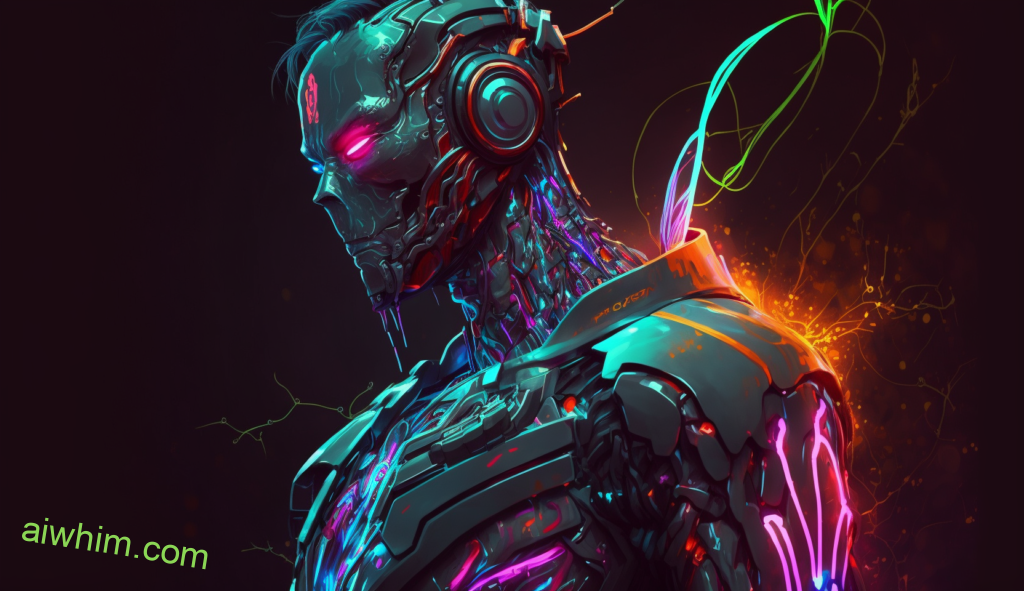
Conclusion
In conclusion, AI and robotics are transforming the manufacturing industry. Automation has been present in factories for decades, but its current capabilities are advancing at a rapid pace. We may soon reach a point where robots and AI can replace many human workers on production lines. This potential displacement could lead to millions of lost jobs, with only minimal replacement positions available. Nevertheless, it is estimated that automation will create up to 14 million new jobs by 2030 which could offset some of these losses.
It’s important to note that while automation is inevitable, there are still ways to help those affected by job loss transition into other industries or roles. Governments should be investing in retraining programs so that they can adequately prepare their citizens for this shift in the labor market. Moreover, businesses must strive towards creating meaningful work opportunities rather than just exploiting cheap labor sources.
Ultimately, we need to accept that technology advancements will continue affecting our lives and plan accordingly if we want to protect our economies from drastic changes brought about by automation. One interesting statistic worth noting is that currently over 500 million people worldwide are employed in manufacturing – an industry set to experience significant transformation due to AI and robotic adoption rates rising rapidly in the near future.
Author: Ole Paulson
Author Bio: I’m Ole and on this website, I share everything there is to know about Artificial Intelligence, and useful tips for using AI to our advantage. I have a background in data science and research and have been following the AI-space for years. You can read more about me in the “About” page.